Refrigeration system could help reduce flaring, generate revenue for western Canadian oil and gas producers
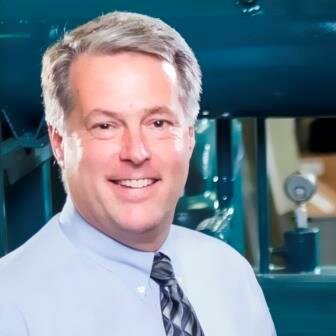
Large photo shows a BERG GTUIT unit with processing capacity of 1 million cubic feet per day.
Small photo is of Don Berggren, President, Berg Chilling Systems
Photo within story is a BERG GTUIT system on site. All photos courtesy Berg Chilling Systems
A Toronto-based company with a refrigeration technology that reduces greenhouse gases at oil gas well sites while recovering valuable natural gas liquids hopes to interest western Canadian producers, after deploying 30 systems in the Bakken oilfield in the United States.
Berg Chilling Systems Inc. and Montana-based partner GTUIT have developed a mobile system that removes heavy hydrocarbons – including propane, butane, hexane and pentane – from an oil and gas stream and leaves a dry, conditioned gas that can be used for onsite power generation or put into a sales gas pipeline. The heavy hydrocarbons, along with any surplus compressed gas, can be trucked away for sale.
The system removes the need to flare or vent gas and also eliminates an operator’s reliance on costly diesel fuel for remote well sites, says Don Berggren, president of Berg Chilling Systems.
“In the world we live in now, there really isn’t a good reason to flare unless there’s an upset [operating] condition,” he says.
“We have a proven, working solution that will drive natural gas liquids dollars to a producer’s bottom line, making them a more profitable and a more environmentally friendly producer.”
Berg Chilling Systems says that in the last three years in the Bakken field, the technology has captured 23 million gallons of natural gas liquids, diverted 5 billion cubic feet of flaring gas, and kept 200,000 tonnes of carbon dioxide out of the atmosphere.
“We’ve got several big operators in the U.S. using the solution, and we know that it would work just as well up here in Canada,” Berggren said.
Flaring, venting on rise in Alberta, B.C.
But oil and gas producers in Canada have not picked up on the technology, even though overall flaring and venting emissions in Alberta and British Columbia recently increased, after declining through most of the past decade.
The combined volume of flared and vented solution gas increased 2.3 per cent in 2014, to 920 million cubic metres compared with 899 cubic metres in 2013, according to the most recent report by the Alberta Energy Regulator. Flaring and venting from oil sands crude bitumen batteries increased by, respectively, 31.2 per cent and 3.5 per cent.
In British Columbia, flaring levels overall increased by 22 per cent, to 236.3 million cubic metres, in 2014 compared with 2013 levels, mainly due to increased exploratory drilling and well testing, according to the most recent report by the BC Oil and Gas Commission.
Berg Chilling Systems and GTUIT are hoping that new regulations to reduce methane emissions and, in Alberta, an increasing carbon levy for large industrial emitters, will attract Canadian producers’ interest in their system.
The Alberta government, under its Climate Leadership Plan, requires that the oil and gas industry reduce its methane emissions by 45 per cent by 2025. Also, Canada, the U.S. and Mexico all agreed in June to cut methane emissions from their oil and gas sectors by 40 to 45 per cent by 2025.
“It shifts everybody’s focus a little bit when the regulatory environment changes,” along with economics and infrastructure considerations, says Jim Haider, chief technology officer for GTUIT.
“We’re excited to see what can be done in your neck of the woods . . . We want to turn this problem into an opportunity so that a lot of people can gain from it.”
New solution developed for horizontal, fracked wells
GTUIT, a full-service gas-processing company, began developing the system a few years ago after flaring became a problem in the Bakken in North Dakota – at one point accounting for one-third of oilfield flaring in the United States.
However, off-the-shelf equipment designed for conventional vertical oil and gas wells couldn’t handle the much higher flow of fluids entrained with oil and gas extracted with horizontal drilling of multiple wells and multi-stage hydraulic fracturing in tight source rock, Haider says. “It’s kind of this big, rich, hydrocarbon stew.”
GTUIT developed and sourced the technologies to control well flow variability and pressure fluctuations and changes in chemistry, and manage the hydrocarbon fluids and other substances in the gas stream, such as water, particulate matter and frack sand. The company also handles gas compression and has proprietary processing-control software.
“We really needed a refrigeration specialist to make our process work and develop the refrigeration capacity in a very small footprint, so we could put it on a truck or a tractor-trailer,” Haider says. “So our partnership with Berg is critical to our success.”
In the U.S., GTUIT owns and operates a large fleet of its own equipment that producers lease as a service to manage their flaring emissions.
One of the larger systems can process 1 million standard cubic feet of well flow per day, and make about four to six gallons of natural gas liquids each day – keeping about 12,000 tons of carbon dioxide per year out of the atmosphere, Haider says. A series of connected systems can handle well pad flows upward of 4 to 5 standard cubic feet of per day.
GTUIT produced about 1.3 million gallons of liquids in August for operators in the U.S., Haider adds. “Each one of gallons of liquids is a whole bunch of hydrocarbons that would have turned into CO2” emitted to the atmosphere.
Other technologies for flare management
GTUIT and Berg’s system isn’t the only player in the flare-management marketplace.
For example, Calgary-based Questor Technology Inc. offers permanent and mobile waste gas incinerators with combustion efficiency in excess of 99.99 per cent. The combusted gas provides heat that can be used in various facility applications.
Another player, Red Deer, Alta.-based Total Combustion Inc., rents mobile and skid-mounted waste gas incinerators.
GE also has developed technology, using gas-fueled turbines, to turn flare gas into power. Calgary-based Genalta Power is another company that offers solutions to turn flare gas into power.
However, GTUIT and Berg’s system is a more ‘upstream’ technology, cleaning up and capturing the saleable natural gas liquids in the raw oil and gas stream, while leaving a dry residue gas which can then be incinerated or used for power generation.
“Most things that generate power can’t tolerate the really ‘crazy’ gas that comes straight out of the ground. It needs to be processed at least to some level, and that’s where we come in,” Haider says. “We generate a pretty big stream of liquids and those liquids go to market.”
“We look at our process as almost like a pre-treatment plant for many of these other solutions,” Berggren says. “We look at it as a complementary technology rather than a competitive one.”
Enerplus using system in Bakken
Berg Chilling Systems, a family-owned business, has provided custom refrigeration and cooling solutions for about 45 years to a wide range of industries, including plastics, automotive, heavy metal stamping, food processing, marine applications and now, petrochemicals and oil and gas.
Chilling a well’s raw oil and gas stream separates the methane from the heavy hydrocarbons which ‘precipitate’ out, Berggren explains.
Producers connected to a sales gas pipeline can send the conditioned residue gas directly to the pipeline. To use the gas for onsite power generation, they would need smaller collection pipelines and a gas-fueled generator set.
A lot of remote wells aren’t connected to a power grid, so they depend heavily on costly diesel fuel, Berggren notes. “They have trucks coming in if not daily then every couple of days to replenish their diesel supply at a tremendous cost, and then right beside that they’ve got a flare burning off all this great gas that could be used to generate the power onsite.”
Enerplus is using the system to reduce flare gas and maintain production on the Fort Berthold Indian Reservation in North Dakota’s Bakken oilfield, according to a December 2015 news release by Caterpillar, a minority owner of GTUIT.
A regulation implemented last year by the North Dakota Industrial Commission requires oil and gas producers to meet a certain percentage of gas capture or have production curtailed to 100 to 200 barrels per day.
“Some of our wells can produce over 1,000 barrels daily, so that’s a significant penalty. Reducing emissions and avoiding curtailment were the key drivers in our decision to look at the GTUIT units,” Norm Robotham, Enerplus team leader for U.S. facilities, said in the release.
The units, which easily connect to an engine or generator set, “significantly decrease the volume of flared gas at the wellhead, reducing the volume of volatile organic compounds released into the atmosphere,” Caterpillar said.
Enerplus at the time had three GTUIT units operating and another on standby. “It’s proven technology available at a good price point, and the units are very mobile so you can move them around as needed,” Robotham said.
Reaching out to Canadian producers
So why aren’t Canadian producers using the system?
Berggren says one reason is the current slump in world oil prices, which resulted in the global petroleum industry cutting capital and operating expenses and employees. “It hasn’t stopped the sales process. But it certainly has put a bit of a lag in it.”
In the U.S., GTUIT’s partnership and marketing agreement with Houston-based Caterpillar Oil and Gas provides access to the U.S. oil and gas industry. GTUIT is developing a relationship with Caterpillar’s Canadian counterpart, Finning Canada. The plan is for Finning to own the flare-management system equipment and lease it to Canadian oil and gas producers.
Haider thinks producers here will be interested in what he calls the system’s “layer-cake” of benefits. “You get liquids for market, you get the ability to generate electricity with the residual gas and offset things like diesel, you get carbon credits if there is a carbon tax for what you’re doing, you get an environmental benefit that includes CO2 reductions in a real meaningful way, and you get VOC (volatile organic compound) reductions. Those value propositions start to add up monetarily to a producer.”
Berggren says his company has sent information to the Canadian Association of Petroleum Producers in Calgary, so CAPP can let its member-companies know about the system. “I think we can help make them good green producers and make money at the same time,” he says.
Related News